Designer & Engineer
Create Your First Project
Start adding your projects to your portfolio. Click on "Manage Projects" to get started
Project Title
Project Type
Photography
Date
April 2023
This is where the project description goes. Give an overview or go in depth - what it’s all about, what inspired you, how you created it, or anything else you’d like visitors to know. To add Project descriptions, go to Manage Projects.
v-1 Prosthetic
Client
Role
Time
Date
Personal
The Designer
5 Weeks
June 2023
100 million people worldwide struggle to attain proper prostheses. This arm utilizes
bio-design and generative processes to adapt to materials and optimize form. Giving those suffering from limb loss an affordable, accessible solution.


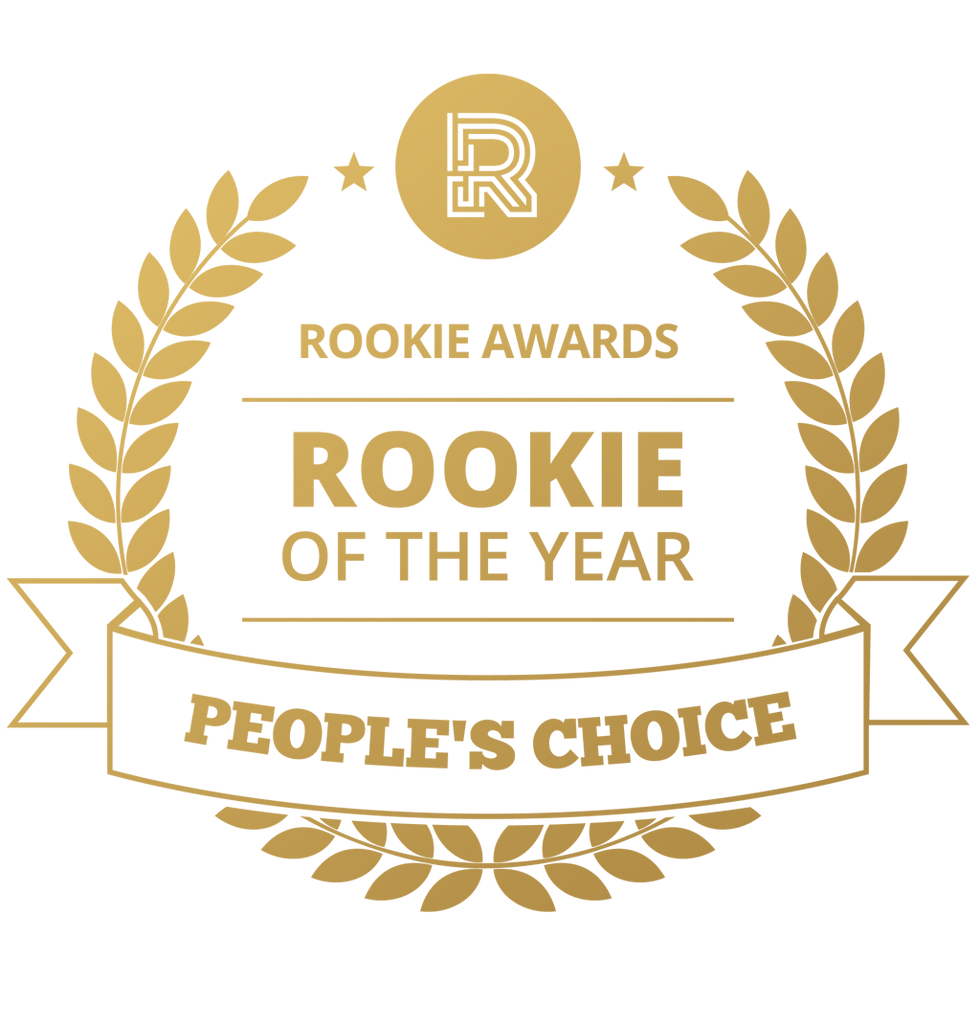



v-1 P

100 million people worldwide need a prosthetic limb. According to the University of South Hampton, around 80 percent of these people don't have access to these services. There are multiple factors that cause this, a major one being socioeconomics. The current prostheses available are too expensive. Low to middle-income countries cannot access these resources. Even high-income countries’ lower-class citizens have to fight for adequate prostheses.
Optimizing form
maintaining strength, reducing material, reducing cost.
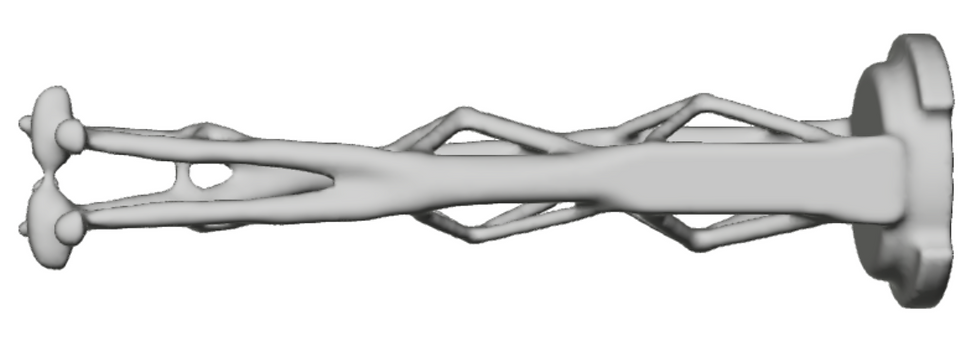.png)
_edited.jpg)
.png)

25%
50%
75%
100%
Implementing generative design, can significantly cut down material volume and create tailor-fit prostheses for each person. By converting a 3D scan of each patient’s arm into a boundary representation, I was able to use fixed force-tolerance parameters that are calibrated to the human arm. Then, generated a raw optimized boundary representation through simulation. Using this modeling process, materials are interchangeable, and the form adapts to each desired material’s properties. These new forms are lightweight and aid in fatigue that other prostheses create. The overall prosthetic form is familiar and will integrate more easily into each person’s life
Methodolgy
Plug in any viable material.
This material choice has impressive tribological properties and the ability to osseointegrate. Using titanium with a positive surface charge will form noncovalent bonds with negatively charged proteins and promote bacterial adhesion which may lead to infections.
The tensile strength of titanium protects it from long-term wear but it is much higher than bone and can lead to local bone atrophy and ultimately aseptic loosening over time, this is known as “stress shielding”, it is a common point of implant failure, and would have to be monitored when using higher-grade titanium.
Benefits and Considerations
This material is a non-cytotoxic metal oxide that is ionic and has no potential for bacterial adhesion. Which protects against implant surface infection. In addition, these are an inert material and exhibit high biocompatibility. Zirconia implants osseointegrate as well as titanium implants and are comparable in strength to weight.
Like titanium implants zirconia has a high tensile strength and may cause effects on local bones over time from “stress shielding”. Studies have also shown increased surface wear of zirconia implants over time when compared to its titanium counterparts.
Benefits and Considerations
This material offers numerous material benefits including reduced wear, high strength-to-weight ratio, a similar elastic modulus to that of bone, and high biocompatibility. Its elasticity reduced stress given on interfacing bones and it is chemically inert, generating no cellular toxicity in in vitro studies.
Carbon Fiber PEEK is also the most accessible additive manufacturing material out of the four and available on multiple printing processes. Considering cost this would be the most affordable option.
Benefits and Considerations
PEKK biomaterials is an elastic material with good shock absorbance and fracture resistance and present ultra-high performance among all thermoplastic composites for excellent mechanical strength, chemical resistance, and high thermal stability. In a dentistry setting PEKK implants have shown lesser stress shielding compared to titanium for dental implant applications. Although PEKK is very promising it has been mostly prevalent in the dentistry industry and would require more study in orthopedic application.
Its availability and printing accessibility is similar to CF-PEEK. Yet, CF-PEEK is currently more widely used as an orthopedic implant material.
Benefits and Considerations
Overview.
Biology Influenced, Easily Upgradable, Permanent Prosthesis
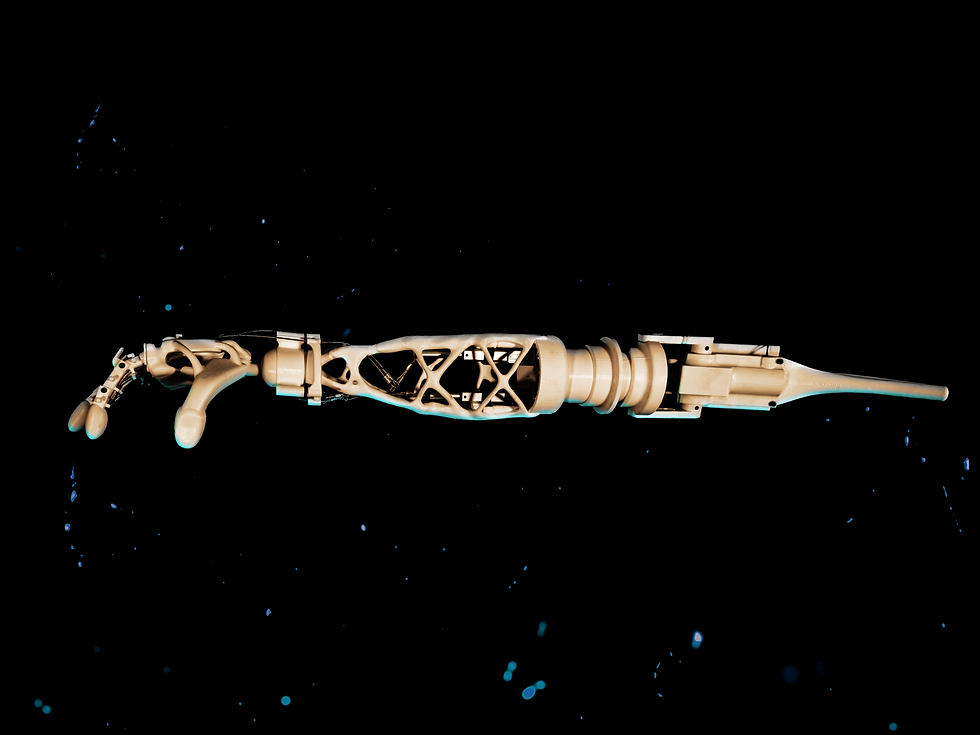
For more natural movements.
Ligament Driven Hand
Protective cage for ligament drivers.
Motor Assembly
ECG Sensor driven for intuitive control.
Bicep Abutment
Remove, rest or upgrade.
Ball Bearing Quick Release

The arm embodies bio-inspired design, drawing parallels to the efficient cell structures observed in Voronoi tessellations inherent in natural formations. In contemplating the methodical approach to the arm's motor functions, a thorough examination of nature's evolution of our motor systems proved immensely valuable. Seeking the most optimal and organic means of generating artificial movement, I mirrored the mechanisms employed by our natural arms. While the v-1 P represents a rudimentary iteration of this approach, current work on the v-2 P aims to delve deeper into this methodology, and improve upon systems akin to those presently available in the market.